Open circuit in Power source circuit (C13A0,C13A5,C13B0)
DESCRIPTION
The following DTCs are stored when a malfunction occurs in the parking brake ECU (brake actuator assembly).
DTC No. | Detection Item |
DTC Detection Condition | Trouble Area |
Memory | Note |
C13A0 | Open circuit in Power source circuit |
Both of following conditions are met:
- Power switch on (IG) or electric parking brake switch (electric parking
brake switch assembly) pulled to lock side with power switch off.
- Parking brake ECU (brake actuator assembly) power source relay circuit is open for approximately 0.5 seconds.
| Parking brake ECU (brake actuator assembly) |
DTC stored | An electric parking brake system malfunction is displayed on the multi-information display. |
C13A5 | Electric Current of Motor |
Both of following conditions are met:
- Power switch on (IG) or electric parking brake switch (electric parking
brake switch assembly) pulled to lock side with power switch off.
- Parking brake ECU (brake actuator assembly) internal current is abnormal
for approximately 0.1 to 0.5 seconds (differs according to
malfunction).
| Parking brake ECU (brake actuator assembly) |
DTC stored | An electric parking brake system malfunction is displayed on the multi-information display. |
C13B0 | Electric Parking Brake ECU Malfunction |
Both of following conditions are met:
- Power switch on (IG) or electric parking brake switch (electric parking
brake switch assembly) pulled to lock side with power switch off.
- Internal current of Parking brake ECU (brake actuator assembly) or ECU
components abnormal for a maximum of 60 seconds (differs according to
malfunction).
| Parking brake ECU (brake actuator assembly) |
DTC stored | An electric parking brake system malfunction is displayed on the multi-information display. |
DTC Detection Conditions: C13A0 |
Vehicle Condition |
Pattern 1 | Pattern 2 |
Diagnosis Condition | Power switch on (IG) |
â—‹ | - |
Electric parking brake switch (electric parking brake switch assembly) pulled to lock side with power switch off |
- | â—‹ |
Malfunction Status | Parking brake ECU (brake actuator assembly)'s power source relay is open |
â—‹ | â—‹ |
Detection Time | Approximately 0.5 seconds |
Approximately 0.5 seconds |
Number of Trips | 1 trip |
1 trip |
HINT:
DTC will be output when conditions for either of the patterns in the table above are met.
DTC Detection Conditions: C13A5 |
Vehicle Condition |
Pattern 1 | Pattern 2 |
Pattern 3 | Pattern 4 |
Diagnosis Condition | Power switch on (IG) |
â—‹ | - |
â—‹ | - |
Electric parking brake switch (electric parking brake switch assembly) pulled to lock side with power switch off |
- | â—‹ |
- | â—‹ |
Malfunction Status | Parking brake ECU (brake actuator assembly)'s internal current is abnormal (When parking brake is operating) |
â—‹ | â—‹ |
- | - |
Parking brake ECU (brake actuator assembly)'s internal current is abnormal (When parking brake is not operating) |
- | - |
â—‹ | â—‹ |
Detection Time | Approximately 0.3 seconds |
Approximately 0.3 seconds |
Approximately 0.5 seconds |
Approximately 0.5 seconds |
Number of Trips | 1 trip |
1 trip | 1 trip |
1 trip |
HINT:
DTC will be output when conditions for either of the patterns in the table above are met.
DTC Detection Conditions: C13B0 |
Vehicle Condition |
Pattern 1 | Pattern 2 |
Pattern 3 | Pattern 4 |
Diagnosis Condition | Power switch on (IG) |
â—‹ | - |
â—‹ | - |
Electric parking brake switch (electric parking brake switch assembly) pulled to lock side with power switch off |
- | â—‹ |
- | â—‹ |
Malfunction Status | Parking brake ECU (brake actuator assembly)'s internal voltage is abnormal |
â—‹ | â—‹ |
- | - |
EEPROM is malfunctioning |
- | - |
â—‹ | â—‹ |
Detection Time | Approximately 0.5 seconds |
Approximately 0.5 seconds |
Approximately 0.5 seconds |
Approximately 0.5 seconds |
Number of Trips | 1 trip |
1 trip | 1 trip |
1 trip |
HINT:
DTC will be output when conditions for either of the patterns in the table above are met.
CAUTION / NOTICE / HINT
NOTICE:
The
parking brake indicator light blinks (red) when the power switch is
turned on (IG) after replacing the parking brake ECU (brake actuator
assembly). Operate the electric parking brake switch (electric parking
brake switch assembly) to turn off the parking brake indicator light
(red).
PROCEDURE
1. | REPLACE PARKING BRAKE ECU (BRAKE ACTUATOR ASSEMBLY) |
(a) Replace the parking brake ECU (brake actuator assembly).
Click here
NEXT | |
END |
Short circuit in Power source circuit (C13A1)
DESCRIPTION
C13A1 is stored if the power supply relay in the parking brake ECU assembly has a short circuit.
C13A1
is stored if the power switch is off and a voltage of 2.5 V or higher
is applied to the IG terminal and an electric parking brake switch
assembly malfunction or wire harness malfunction between the switch and
ECU occurs.
DTC No. | Detection Item |
DTC Detection Condition | Trouble Area |
Memory | Note |
C13A1 | Short circuit in Power source circuit |
Both of following conditions are met:
- Electric parking brake switch (electric parking brake switch assembly) pulled to lock side with power switch off.
- Parking brake ECU (brake actuator assembly) power source relay shorted for approximately 60 seconds.
|
- Wire harness or connector
- Electric parking brake switch (electric parking brake switch assembly)
- Parking brake ECU (brake actuator assembly)
| DTC stored |
An electric parking brake system malfunction is displayed on the multi-information display. |
WIRING DIAGRAM
CAUTION / NOTICE / HINT
NOTICE:
- Inspect the fuses for circuits related to this system before performing the following procedure.
- The electric parking brake may still operate up to 20 seconds after the
power switch is turned off. Before disconnecting connectors or fuses,
turn the power switch off and wait 20 seconds or more.
- The parking brake indicator light blinks (red) when the power switch is
turned on (IG) after replacing the parking brake ECU (brake actuator
assembly). Operate the electric parking brake switch (electric parking
brake switch assembly) to turn off the parking brake indicator light
(red).
PROCEDURE
1. | CHECK HARNESS AND CONNECTOR (BEPB CIRCUIT) |
*a | Front view of wire harness connector (to Parking Brake ECU (Brake Actuator Assembly)) |
(a) Turn the power switch off.
(b) Disconnect the A39 parking brake ECU (brake actuator assembly) connector.
(c) Measure the voltage according to the value(s) in the table below.
Standard Voltage:
Tester Connection | Condition |
Specified Condition |
A39-9 (BEPB) - Body ground |
Power switch off | 11 to 14 V |
NG |
| REPAIR OR REPLACE HARNESS OR CONNECTOR |
OK |
| |
2. |
CHECK HARNESS AND CONNECTOR (PARKING BRAKE ECU (BRAKE ACTUATOR ASSEMBLY) - IG POWER SOURCE CIRCUIT) |
*a | Front view of wire harness connector
(to Parking Brake ECU (Brake Actuator Assembly)) |
(a) Turn the power switch off.
(b) Disconnect the A39 parking brake ECU (brake actuator assembly) connector.
(c) Measure the voltage according to the value(s) in the table below.
Standard Voltage:
Tester Connection | Condition |
Specified Condition |
A39-26 (IG) - Body ground |
Power switch off | Below 2.5 V |
NG |
| REPAIR OR REPLACE HARNESS OR CONNECTOR |
OK |
| |
3. |
INSPECT ELECTRIC PARKING BRAKE SWITCH (ELECTRIC PARKING BRAKE SWITCH ASSEMBLY) |
(a) Remove the electric parking brake switch (electric parking brake switch assembly).
Click here
(b) Inspect the electric parking brake switch (electric parking brake switch assembly).
Click here
NG |
| REPLACE ELECTRIC PARKING BRAKE SWITCH (ELECTRIC PARKING BRAKE SWITCH ASSEMBLY) |
OK |
| |
4. |
CHECK
HARNESS AND CONNECTOR (PARKING BRAKE ECU (BRAKE ACTUATOR ASSEMBLY) -
ELECTRIC PARKING BRAKE SWITCH (ELECTRIC PARKING BRAKE SWITCH ASSEMBLY)) |
*a | Front view of wire harness connector
(to Parking Brake ECU (Brake Actuator Assembly)) |
(a) Disconnect the G24 electric parking brake switch (electric parking brake switch assembly) connector.
(b) Disconnect the A39 parking brake ECU (brake actuator assembly) connector.
(c) Measure the resistance according to the value(s) in the table below.
Standard Resistance:
Tester Connection | Condition |
Specified Condition |
A39-14 (SWI1) - Body ground |
Always | 10 kΩ or higher |
A39-20 (SWO1) - Body ground |
Always | 10 kΩ or higher |
A39-24 (SWI2) - Body ground |
Always | 10 kΩ or higher |
A39-22 (SWO2) - Body ground |
Always | 10 kΩ or higher |
OK |
| REPLACE PARKING BRAKE ECU (BRAKE ACTUATOR ASSEMBLY) |
NG |
| REPAIR OR REPLACE HARNESS OR CONNECTOR |
Engine Switch/Power Switch Malfunction (C13A2)
DESCRIPTION
When the power
switch is turned on (IG), power is supplied to the parking brake ECU
(brake actuator assembly). This DTC is stored if IG power source voltage
is not supplied to the parking brake ECU (brake actuator assembly) when
communication with other ECUs is established.
DTC No. | Detection Item |
DTC Detection Condition | Trouble Area |
Memory | Note |
C13A2 | Engine Switch/Power Switch Malfunction |
Both of following conditions are met:
- Power switch on (IG)
- When hybrid vehicle control ECU communicates with main body ECU
(multiplex network body ECU) via CAN communication, IG power supply
voltage is not received for approximately 15 seconds.
|
- Wire harness or connector
- IG power source circuit
- Parking brake ECU (brake actuator assembly)
| DTC stored |
An electric parking brake system malfunction is displayed on the multi-information display. |
WIRING DIAGRAM
CAUTION / NOTICE / HINT
NOTICE:
- Inspect the fuses for circuits related to this system before performing the following procedure.
- The electric parking brake may still operate up to 20 seconds after the
power switch is turned off. Before disconnecting connectors or fuses,
turn the power switch off and wait 20 seconds or more.
- The parking brake indicator light blinks (red) when the power switch is
turned on (IG) after replacing the parking brake ECU (brake actuator
assembly). Operate the electric parking brake switch (electric parking
brake switch assembly) to turn off the parking brake indicator light
(red).
PROCEDURE
1. | READ VALUE USING TECHSTREAM (IG SWITCH) |
(a) Turn the power switch off.
(b) Connect the Techstream to the DLC3.
(c) Turn the power switch on (IG).
(d) Turn the Techstream on.
(e) Enter the following menus: Chassis / Electric Parking Brake / Data List.
(f) Read the Data List according to the display on the Techstream.
Chassis > Electric Parking Brake > Data List
Tester Display | Measurement Item |
Range | Normal Condition |
Diagnostic Note |
IG Switch | IG power source status |
OFF or ON | OFF: IG power source voltage is not input to skid control ECU (brake booster with master cylinder assembly)
ON: IG power source voltage is input to skid control ECU (brake booster with master cylinder assembly) |
- |
Chassis > Electric Parking Brake > Data List
NG |
| GO TO STEP 3 |
OK |
| |
(a) Clear the DTCs.
Chassis > Electric Parking Brake > Clear DTCs
(b) Turn the power switch off.
(c) Check for DTCs.
Chassis > Electric Parking Brake > Trouble Codes
Result |
Proceed to |
DTCs are output |
A |
DTCs are not output |
B |
A |
| REPLACE PARKING BRAKE ECU (BRAKE ACTUATOR ASSEMBLY) |
B |
| USE SIMULATION METHOD TO CHECK |
3. |
CHECK HARNESS AND CONNECTOR (PARKING BRAKE ECU (BRAKE ACTUATOR ASSEMBLY) - POWER SOURCE AND BODY GROUND) |
*a | Front view of wire harness connector
(to Parking Brake ECU (Brake Actuator Assembly)) |
(a) Disconnect the A39 parking brake ECU (brake actuator assembly) connectors.
(b) Turn the power switch on (IG).
(c) Measure the voltage according to the value(s) in the table below.
Standard Voltage:
Tester Connection | Condition |
Specified Condition |
A39-26 (IG) - Body ground |
Power switch on (IG) |
8 to 16 V |
(d) Turn the power switch off.
(e) Measure the resistance according to the value(s) in the table below.
Standard Resistance:
Tester Connection | Condition |
Specified Condition |
A39-2 (EGND) - Body ground |
Always | Below 1 Ω |
OK |
| REPAIR IG POWER SOURCE CIRCUIT |
NG |
| REPAIR OR REPLACE HARNESS OR CONNECTOR |
Open or Short Circuit in Motor (C13A6)
DESCRIPTION
DTC No. | Detection Item |
DTC Detection Condition | Trouble Area |
Memory | Note |
C13A6 | Open or Short Circuit in Motor |
Both of following conditions are met:
- Power switch on (IG) or electric parking brake switch (electric parking
brake switch assembly) pulled to lock side with power switch off.
- Power supply voltage and +B voltage are normal, but parking brake motor
circuit is malfunctioning for approximately 1 to 2 seconds.
|
- Parking brake actuator assembly
- Wire harness or connector
- Parking brake ECU (brake actuator assembly)
| DTC stored |
An electric parking brake system malfunction is displayed on the multi-information display. |
DTC Detection Conditions |
Vehicle Condition |
Pattern 1 | Pattern 2 |
Diagnosis Condition | Power switch on (IG) |
â—‹ | - |
Electric parking brake switch (electric parking brake switch assembly) pulled to lock side with power switch off |
- | â—‹ |
Malfunction Status | Voltage of power supplied to ECU is normal but malfunction exists in parking brake motor circuit |
â—‹ | â—‹ |
Detection Time | Approximately 1 to 2 seconds |
Approximately 1 to 2 seconds |
Number of Trips | 1 trip |
1 trip |
HINT:
DTC will be output when conditions for either of the patterns in the table above are met.
WIRING DIAGRAM
CAUTION / NOTICE / HINT
NOTICE:
- The electric parking brake may still operate up to 20 seconds after the
power switch is turned off. Before disconnecting connectors or fuses,
turn the power switch off and wait 20 seconds or more.
- The parking brake indicator light blinks (red) when the power switch is
turned on (IG) after replacing the parking brake ECU (brake actuator
assembly). Operate the electric parking brake switch (electric parking
brake switch assembly) to turn off the parking brake indicator light
(red).
PROCEDURE
1. | READ VALUE USING TECHSTREAM (PERMISSION OF RH INTERLOCKING PKB LOCK / PERMISSION OF LH INTERLOCKING PKB LOCK) |
(a) Turn the power switch off.
(b) Connect the Techstream to the DLC3.
(c) Turn the power switch on (IG).
(d) Turn the Techstream on.
(e) Enter the following menus: Chassis / Electric Parking Brake / Data List.
(f) Read the Data List according to the display on the Techstream.
Chassis > Electric Parking Brake > Data List
Tester Display | Measurement Item |
Range | Normal Condition |
Diagnostic Note |
Permission of RH Interlocking PKB Lock |
Parking brake actuator assembly RH parking brake lock control permission status |
OK or NG | OK |
- |
Permission of LH Interlocking PKB Lock |
Parking brake actuator assembly RH parking brake lock control permission status |
OK or NG | OK |
- |
Chassis > Electric Parking Brake > Data List
Tester Display |
Permission of RH Interlocking PKB Lock |
Permission of LH Interlocking PKB Lock |
NEXT |
| |
2. |
INSPECT PARKING BRAKE WIRE ASSEMBLY |
*A | RH |
*B | LH |
*a | Front view of Parking Brake Wire Assembly |
*b | (to wire harness connector) |
*c | (to Parking Brake Actuator Assembly) |
- | - |
(a) Turn the engine switch off.
(b) Make sure that there is no looseness at the locking part and the connecting part of the connectors.
OK:
The connector is securely connected.
(c) Remove the parking brake wire assembly.
(d) Check both the connector case and the terminals for deformation and corrosion.
OK:
No deformation or corrosion.
(e) Inspect the parking brake wire assembly.
Standard Resistance:
RH
Tester Connection | Condition |
Specified Condition |
YK1-1 (MRR-) - Y4-1 (RE-) |
Always | Below 1 Ω |
YK1-1 (MRR-) or Y4-1 (RE-) - Body ground and other terminals |
Always | 10 kΩ or higher |
YK1-2 (MRR+) - Y4-2 (RE+) |
Always | Below 1 Ω |
YK1-2 (MRR+) or Y4-2 (RE+) - Body ground and other terminals |
Always | 10 kΩ or higher |
LH
Tester Connection | Condition |
Specified Condition |
YK2-1 (MRL-) - Y1-1 (LE-) |
Always | Below 1 Ω |
YK2-1 (MRL-) or Y1-1 (LE-) - Body ground and other terminals |
Always | 10 kΩ or higher |
YK2-2 (MRL+) - Y1-2 (LE+) |
Always | Below 1 Ω |
YK2-2 (MRL+) or Y1-2 (LE+) - Body ground and other terminals |
Always | 10 kΩ or higher |
NG |
| REPLACE PARKING BRAKE WIRE ASSEMBLY |
OK |
| |
3. |
CHECK HARNESS AND CONNECTOR (PARKING BRAKE ECU (BRAKE ACTUATOR ASSEMBLY) - PARKING BRAKE ACTUATOR ASSEMBLY) |
(a) Turn the power switch off.
(b) Make sure the parking brake wire assembly is securely installed.
(c) Disconnect the A39 parking brake ECU (brake actuator assembly) connector.
(d) Disconnect the Y4 or Y1 parking brake actuator assembly connector.
(e) Measure the resistance according to the value(s) in the table below.
Standard Resistance:
RH
Tester Connection | Condition |
Specified Condition |
A39-4 (MRR+) - Y4-2 (RE+) |
Always | Below 1 Ω |
A39-3 (MRR-) - Y4-1 (RE-) |
Always | Below 1 Ω |
A39-4 (MRR+) or Y4-2 (RE+) - Body ground |
Always | 10 kΩ or higher |
A39-3 (MRR-) or Y4-1 (RE-) - Body ground |
Always | 10 kΩ or higher |
LH
Tester Connection | Condition |
Specified Condition |
A39-7 (MRL+) - Y1-2 (LE+) |
Always | Below 1 Ω |
A39-8 (MRL-) - Y1-1 (LE-) |
Always | Below 1 Ω |
A39-7 (MRL+) or Y1-2 (LE+) - Body ground |
Always | 10 kΩ or higher |
A39-8 (MRL-) or Y1-1 (LE-) - Body ground |
Always | 10 kΩ or higher |
NG |
| REPAIR OR REPLACE HARNESS OR CONNECTOR |
OK |
| |
4. |
INSPECT PARKING BRAKE ACTUATOR ASSEMBLY |
(a) Remove the parking brake actuator assembly.
Click here
(b) Inspect the parking brake actuator assembly.
Click here
OK |
| REPLACE PARKING BRAKE ECU (BRAKE ACTUATOR ASSEMBLY) |
NG |
| REPLACE PARKING BRAKE ACTUATOR ASSEMBLY |
Actuator Malfunction (C13A7)
DESCRIPTION
DTC No. | Detection Item |
DTC Detection Condition | Trouble Area |
Memory | Note |
C13A7 | Actuator Malfunction |
Both of following conditions are met:
- Electric parking brake is operating
- One of following is detected: Motor lock, gear lock, motor spinning or repeated slipping
|
- Parking brake actuator assembly
- Rear brake
- Wire harness or connector
| DTC stored |
An electric parking brake system malfunction is displayed on the multi-information display. |
DTC Detection Conditions |
Vehicle Condition |
Pattern 1 | Pattern 2 |
Pattern 3 | Pattern 4 |
Diagnosis Condition | Electric parking brake is operating |
â—‹ | â—‹ |
â—‹ | â—‹ |
Malfunction Status | Motor lock is detected |
â—‹ | - |
- | - |
Gear lock is detected |
- | â—‹ |
- | - |
Motor spinning is detected |
- | - |
â—‹ | - |
Repeated slipping is detected |
- | - |
- | â—‹ |
Detection Time | - |
- | - |
- |
Number of Trips | 1 trip |
1 trip | 1 trip |
1 trip |
HINT:
DTC will be output when conditions for either of the patterns in the table above are met.
WIRING DIAGRAM
Click here
CAUTION / NOTICE / HINT
NOTICE:
- This DTC may be stored when the system changes to pad replacement mode, but this is not a malfunction.
- This DTC may be stored when the parking brake is forcibly released, but this is not a malfunction.
- The electric parking brake may still operate up to 20 seconds after the
power switch is turned off. Before disconnecting connectors or fuses,
turn the power switch off and wait 20 seconds or more.
- The parking brake indicator light blinks (red) when the power switch is
turned on (IG) after replacing the parking brake ECU (brake actuator
assembly). Operate the electric parking brake switch (electric parking
brake switch assembly) to turn off the parking brake indicator light
(red).
PROCEDURE
(a) Check for DTCs.
Click here
Chassis > Electric Parking Brake > Trouble Codes
Result |
Proceed to |
Only DTC C13A7 is output |
A |
DTCs other than C13A7 are output |
B |
B |
| GO TO DIAGNOSTIC TROUBLE CODE CHART |
A |
| |
2. |
READ VALUE USING TECHSTREAM (PERMISSION OF RH INTERLOCKING PKB LOCK / PERMISSION OF LH INTERLOCKING PKB LOCK) |
(a) Turn the power switch off.
(b) Connect the Techstream to the DLC3.
(c) Turn the power switch on (IG).
(d) Turn the Techstream on.
(e) Enter the following menus: Chassis / Electric Parking Brake / Data List.
(f) Read the Data List according to the display on the Techstream.
Chassis > Electric Parking Brake > Data List
Tester Display | Measurement Item |
Range | Normal Condition |
Diagnostic Note |
Permission of RH Interlocking PKB Lock |
Parking brake actuator assembly RH parking brake lock control permission status |
OK or NG | OK |
- |
Permission of LH Interlocking PKB Lock |
Parking brake actuator assembly RH parking brake lock control permission status |
OK or NG | OK |
- |
Chassis > Electric Parking Brake > Data List
Tester Display |
Permission of RH Interlocking PKB Lock |
Permission of LH Interlocking PKB Lock |
NEXT |
| |
3. |
INSPECT PARKING BRAKE WIRE ASSEMBLY |
*A | RH |
*B | LH |
*a | Front view of Parking Brake Wire Assembly |
*b | (to wire harness connector) |
*c | (to Parking Brake Actuator Assembly) |
- | - |
(a) Turn the engine switch off.
(b) Make sure that there is no looseness at the locking part and the connecting part of the connectors.
OK:
The connector is securely connected.
(c) Remove the parking brake wire assembly.
(d) Check both the connector case and the terminals for deformation and corrosion.
OK:
No deformation or corrosion.
(e) Inspect the parking brake wire assembly.
Standard Resistance:
RH
Tester Connection | Condition |
Specified Condition |
YK1-1 (MRR-) - Y4-1 (RE-) |
Always | Below 1 Ω |
YK1-1 (MRR-) or Y4-1 (RE-) - Body ground and other terminals |
Always | 10 kΩ or higher |
YK1-2 (MRR+) - Y4-2 (RE+) |
Always | Below 1 Ω |
YK1-2 (MRR+) or Y4-2 (RE+) - Body ground and other terminals |
Always | 10 kΩ or higher |
LH
Tester Connection | Condition |
Specified Condition |
YK2-1 (MRL-) - Y1-1 (LE-) |
Always | Below 1 Ω |
YK2-1 (MRL-) or Y1-1 (LE-) - Body ground and other terminals |
Always | 10 kΩ or higher |
YK2-2 (MRL+) - Y1-2 (LE+) |
Always | Below 1 Ω |
YK2-2 (MRL+) or Y1-2 (LE+) - Body ground and other terminals |
Always | 10 kΩ or higher |
NG |
| REPLACE PARKING BRAKE WIRE ASSEMBLY |
OK |
| |
4. |
CHECK HARNESS AND CONNECTOR (PARKING BRAKE ECU (BRAKE ACTUATOR ASSEMBLY) - PARKING BRAKE ACTUATOR ASSEMBLY) |
(a) Turn the power switch off.
(b) Make sure the parking brake wire assembly is securely installed.
(c) Disconnect the A39 parking brake ECU (brake actuator assembly) connector.
(d) Disconnect the Y4 or Y1 parking brake actuator assembly connector.
(e) Measure the resistance according to the value(s) in the table below.
Standard Resistance:
RH
Tester Connection | Condition |
Specified Condition |
A39-4 (MRR+) - Y4-2 (RE+) |
Always | Below 1 Ω |
A39-3 (MRR-) - Y4-1 (RE-) |
Always | Below 1 Ω |
A39-4 (MRR+) or Y4-2 (RE+) - Body ground |
Always | 10 kΩ or higher |
A39-3 (MRR-) or Y4-1 (RE-) - Body ground |
Always | 10 kΩ or higher |
LH
Tester Connection | Condition |
Specified Condition |
A39-7 (MRL+) - Y1-2 (LE+) |
Always | Below 1 Ω |
A39-8 (MRL-) - Y1-1 (LE-) |
Always | Below 1 Ω |
A39-7 (MRL+) or Y1-2 (LE+) - Body ground |
Always | 10 kΩ or higher |
A39-8 (MRL-) or Y1-1 (LE-) - Body ground |
Always | 10 kΩ or higher |
NG |
| REPAIR OR REPLACE HARNESS OR CONNECTOR |
OK |
| |
5. |
INSPECT REAR BRAKE AND PARKING BRAKE ACTUATOR ASSEMBLY |
(a) Enter rear brake pad replacement mode.
Click here
(b) Turn the power switch off.
(c) Check that the rotating parts are not seized or the actuator is not spinning freely.
(1)
Check that the parking brake actuator assembly is installed properly to
the rear brake caliper and that it is not spinning freely.
For the parking brake actuator assembly removal procedure: Click here
(2) Check that there is no damage to the rotating parts from the parking brake actuator assembly to the rear brake caliper.
(3) Inspect the parking brake actuator assembly and check that it operates correctly.
Click here
(4) Check that the rear brake caliper threaded part rotates and that the rear disc brake piston moves outward.
HINT:
For the check procedures, refer to the parking brake forced release method when not using the Techstream.
Click here
HINT:
Return to normal mode after work is complete.
Click here
OK |
| REPLACE PARKING BRAKE ACTUATOR ASSEMBLY |
NG |
| REPAIR OR REPLACE NECESSARY PARTS |
Brake System Malfunction (C13A9)
DESCRIPTION
The parking
brake ECU (brake actuator assembly) receives the wheel speed signal of
each wheel from the skid control ECU (brake booster with master cylinder
assembly) via CAN communication.
This DTC is stored when a malfunction occurs in the skid control ECU (brake booster with master cylinder assembly).
DTC No. | Detection Item |
DTC Detection Condition | Trouble Area |
Memory | Note |
C13A9 | Brake System Malfunction |
Both of following conditions are met:
- Power switch on (IG)
- Malfunction signal is received from skid control ECU (brake booster with
master cylinder assembly) for approximately 0.3 seconds.
|
- Skid control ECU (brake booster with master cylinder assembly)
- Parking brake ECU (brake actuator assembly)
| DTC stored |
An electric parking brake system malfunction is displayed on the multi-information display. |
CAUTION / NOTICE / HINT
NOTICE:
The
parking brake indicator light blinks (red) when the power switch is
turned on (IG) after replacing the parking brake ECU (brake actuator
assembly). Operate the electric parking brake switch (electric parking
brake switch assembly) to turn off the parking brake indicator light
(red).
PROCEDURE
1. | CHECK DTC (ELECTRONICALLY CONTROLLED BRAKE SYSTEM) |
(a) Check for DTCs.
Chassis > ABS/VSC/TRAC > Trouble Codes
Result |
Proceed to |
DTCs are not output |
A |
DTCs are output |
B |
B |
| GO TO ELECTRONICALLY CONTROLLED BRAKE SYSTEM |
A |
| |
2. |
CHECK DTC (ELECTRIC PARKING BRAKE SYSTEM) |
(a) Clear the DTCs.
Chassis > Electric Parking Brake > Clear DTCs
(b) Turn the power switch off.
(c) Check for DTCs.
Chassis > Electric Parking Brake > Trouble Codes
Result |
Proceed to |
DTCs are output |
A |
DTCs are not output |
B |
A |
| REPLACE PARKING BRAKE ECU (BRAKE ACTUATOR ASSEMBLY) |
B |
| USE SIMULATION METHOD TO CHECK |
EPB High Temperature (C13AA)
DESCRIPTION
If the electric
parking brake is used continuously, system operation is stopped to
prevent the parking brake actuator assembly from overheating.
This
DTC is stored when system operation is stopped to prevent the parking
brake actuator assembly from overheating and is not a malfunction.
DTC No. | Detection Item |
DTC Detection Condition | Trouble Area |
Memory | Note |
C13AA | EPB High Temperature |
Both of following conditions are met:
- Electric parking brake is operating
- Lock and release operations are performed 10 times without 2 seconds
periods of no operation; or lock and release operations are performed 5
times without 2 seconds periods of no operation, and target current is
not applied during lock control
| Overheat due to continuous use of system |
DTC stored | A
warning is displayed on the multi-information display indicating
electric parking brake system operation is stopped due to high
temperatures. |
DTC Detection Conditions |
Vehicle Condition |
Pattern 1 | Pattern 2 |
Diagnosis Condition | Electric parking brake is operating |
â—‹ | â—‹ |
Malfunction Status | Lock and release operations are performed without 2 seconds interval 10 times |
â—‹ | - |
Lock
and release operations are performed without 2 seconds interval 5
times, and target current is not achieved during lock control |
- | â—‹ |
Detection Time | - |
- |
Number of Trips | 1 trip |
1 trip |
HINT:
DTC will be output when conditions for either of the patterns in the table above are met.
PROCEDURE
1. |
ELECTRIC PARKING BRAKE OVERHEAT |
(a) With the overheat warning displayed on the multi-information display, wait for approximately 1 minute.
(b) Check that the overheat warning has disappeared.
HINT:
- Check the display after turning the power switch off and on (IG).
- After the warning has disappeared and the electric parking brake system returns to normal, clear the DTCs.
Chassis > Electric Parking Brake > Clear DTCs
NEXT |
| END |
System information not received (C13AE)
DESCRIPTION
DTC No. | Detection Item |
DTC Detection Condition | Trouble Area |
Memory | Note |
C13AE | System information not received |
Both of following conditions are met:
- Power switch on (IG)
- When power switch is first turned on (IG) after parking brake ECU (brake
actuator assembly) has been replaced, system cannot communicate with
hybrid vehicle control ECU for approximately 4 seconds
|
- Hybrid vehicle control ECU
- CAN communication system
- Parking brake ECU (brake actuator assembly)
| DTC stored |
An electric parking brake system malfunction is displayed on the multi-information display. |
CAUTION / NOTICE / HINT
NOTICE:
The
parking brake indicator light blinks (red) when the power switch is
turned on (IG) after replacing the parking brake ECU (brake actuator
assembly). Operate the electric parking brake switch (electric parking
brake switch assembly) to turn off the parking brake indicator light
(red).
PROCEDURE
(a) Turn the power switch off.
(b) Connect the Techstream to the DLC3.
(c) Turn the power switch on (IG).
(d) Turn the Techstream on.
(e) Check for DTC.
Chassis > Electric Parking Brake > Trouble Codes
Result | Proceed to |
DTC C13AE and a CAN DTC are output at the same time |
A |
DTC C13AE is output and the MIL is illuminated |
B |
Only DTC C13AE is output |
C |
DTCs are not output |
D |
A |
| GO TO CAN COMMUNICATION SYSTEM |
B |
| GO TO HYBRID CONTROL SYSTEM |
C |
| REPLACE PARKING BRAKE ECU (BRAKE ACTUATOR ASSEMBLY) |
D |
| USE SIMULATION METHOD TO CHECK |
EPB Switch Malfunction (C13B4)
DESCRIPTION
When the
electric parking brake switch is pulled, a lock request signal is sent
from the parking brake ECU (brake actuator assembly) to the parking
brake actuator assembly. When the electric parking brake switch is
pushed, a release request signal is sent from the parking brake ECU
(brake actuator assembly) to the parking brake actuator assembly.
DTC No. | Detection Item |
DTC Detection Condition | Trouble Area |
Memory | Note |
C13B4 | EPB Switch Malfunction |
- Parking brake switch open or short circuit is detected for 1 second or more
- Parking brake switch stuck malfunction
|
- Electric parking brake switch (electric parking brake switch assembly)
- Wire harness or connector
- Parking brake ECU (brake actuator assembly)
| DTC stored |
An electric parking brake system malfunction is displayed on the multi-information display. |
DTC Detection Conditions |
Vehicle Condition |
Pattern 1 | Pattern 2 |
Diagnosis Condition | - |
- | - |
Malfunction Status | Parking brake switch open or short circuit is detected |
â—‹ | - |
Parking brake switch stuck malfunction |
- | â—‹ |
Detection Time | 1 second or more |
- |
Number of Trips | 1 trip |
1 trip |
WIRING DIAGRAM
CAUTION / NOTICE / HINT
NOTICE:
- The electric parking brake may still operate up to 20 seconds after the
power switch is turned off. Before disconnecting connectors or fuses,
turn the power switch off and wait 20 seconds or more.
- The parking brake indicator light blinks (red) when the power switch is
turned on (IG) after replacing the parking brake ECU (brake actuator
assembly). Operate the electric parking brake switch (electric parking
brake switch assembly) to turn off the parking brake indicator light
(red).
PROCEDURE
1. | INSPECT ELECTRIC PARKING BRAKE SWITCH (ELECTRIC PARKING BRAKE SWITCH ASSEMBLY) |
(a) Inspect the electric parking brake switch (electric parking brake switch assembly).
Click here
NG |
| REPLACE ELECTRIC PARKING BRAKE SWITCH (ELECTRIC PARKING BRAKE SWITCH ASSEMBLY) |
OK |
| |
2. |
CHECK
HARNESS AND CONNECTOR (PARKING BRAKE ECU (BRAKE ACTUATOR ASSEMBLY) -
ELECTRIC PARKING BRAKE SWITCH (ELECTRIC PARKING BRAKE SWITCH ASSEMBLY)) |
(a) Disconnect the G24 electric parking brake switch (electric parking brake switch assembly) connector.
(b) Disconnect the A39 parking brake ECU (brake actuator assembly) connector.
(c) Measure the resistance according to the value(s) in the table below.
Standard Resistance:
Tester Connection | Condition |
Specified Condition |
A39-14 (SWI1) - G24-9 (SWI1) |
Always | Below 1 Ω |
A39-20 (SWO1) - G24-10 (SWO1) |
Always | Below 1 Ω |
A39-24 (SWI2) - G24-1 (SWI2) |
Always | Below 1 Ω |
A39-22 (SWO2) - G24-2 (SWO2) |
Always | Below 1 Ω |
A39-14 (SWI1) or G24-9 (SWI1) - Body ground |
Always | 10 kΩ or higher |
A39-20 (SWO1) or G24-10 (SWO1) - Body ground |
Always | 10 kΩ or higher |
A39-24 (SWI2) or G24-1 (SWI2) - Body ground |
Always | 10 kΩ or higher |
A39-22 (SWO2) or G24-2 (SWO2) - Body ground |
Always | 10 kΩ or higher |
NG |
| REPAIR OR REPLACE HARNESS OR CONNECTOR |
OK |
| |
(a) Clear the DTCs.
Chassis > Electric Parking Brake > Clear DTCs
(b) Turn the power switch off.
(c) Turn the power switch on (IG).
(d) Check for DTCs.
Chassis > Electric Parking Brake > Trouble Codes
Result |
Proceed to |
DTCs are output |
A |
DTCs are not output |
B |
A |
| REPLACE PARKING BRAKE ECU (BRAKE ACTUATOR ASSEMBLY) |
B |
| USE SIMULATION METHOD TO CHECK |
Deceleration Sensor (C1245)
DESCRIPTION
The parking
brake ECU (brake actuator assembly) receives vehicle tilt angle
information from the deceleration sensor (airbag ECU assembly) via CAN
communication.
DTC No. | Detection Item |
DTC Detection Condition | Trouble Area |
Memory | Note |
C1245 | Deceleration Sensor |
One of following conditions is met:
- An error signal is sent from deceleration sensor (airbag ECU assembly) for approximately 0.3 seconds.
- While the deceleration sensor (airbag ECU assembly) signal is judged to
be stuck, starting off and stopping of vehicle occurs 16 times.
- Comparison error between deceleration sensor (airbag ECU assembly) 1 and
deceleration sensor (airbag ECU assembly) 2 output values occurs for 60
seconds or more.
| Deceleration sensor (Airbag ECU assembly) |
DTC stored | An electric parking brake system malfunction is displayed on the multi-information display. |
DTC Detection Conditions |
Vehicle Condition |
Pattern 1 | Pattern 2 |
Pattern 3 |
Diagnosis Condition | Power switch on (IG) |
â—‹ | â—‹ |
â—‹ |
Malfunction Status | An error signal is sent from the deceleration sensor (airbag ECU assembly) |
â—‹ | - |
- |
While
the deceleration sensor (airbag ECU assembly) signal is judged to be
stuck, starting off and stopping the vehicle occurs 16 times |
- | â—‹ |
- |
Comparison
error between deceleration sensor (airbag ECU assembly) 1 and
deceleration sensor (airbag ECU assembly) 2 output values occurs |
- | - |
â—‹ |
Detection Time | Approximately 0.3 seconds |
- | 60 seconds or more |
Number of Trips | 1 trip |
1 trip | 1 trip |
HINT:
DTC will be output when conditions for either of the patterns in the table above are met.
CAUTION / NOTICE / HINT
NOTICE:
When
replacing the deceleration sensor (airbag ECU assembly), perform
initialization and calibration of the linear solenoid valve.
Click here
PROCEDURE
1. |
CHECK DTC (ELECTRONICALLY CONTROLLED BRAKE SYSTEM) |
(a) Check for DTCs.
Chassis > ABS/VSC/TRAC > Trouble Codes
Result | Proceed to |
DTC is not output | A |
DTC is output | B |
B |
| GO TO ELECTRONICALLY CONTROLLED BRAKE SYSTEM |
A |
| |
2. |
CHECK DTC (ELECTRIC PARKING BRAKE SYSTEM) |
(a) Clear the DTCs.
Chassis > Electric Parking Brake > Clear DTCs
(b) Turn the power switch off.
(c) Check for DTCs.
Chassis > Electric Parking Brake > Trouble Codes
Result | Proceed to |
DTCs are output | A |
DTCs are not output | B |
A |
| REPLACE AIRBAG ECU ASSEMBLY |
B |
| USE SIMULATION METHOD TO CHECK |
Data List / Active Test
DATA LIST / ACTIVE TEST
READ DATA LIST
HINT:
Using
the Techstream to read the Data List allows the values or states of
switches, sensors, actuators and other items to be read without removing
any parts. This non-intrusive inspection can be very useful because
intermittent conditions or signals may be discovered before parts or
wiring is disturbed. Reading the Data List information early in
troubleshooting is one way to save diagnostic time.
NOTICE:
In
the table below, the values listed under "Normal Condition" are
reference values. Do not depend solely on these reference values when
deciding whether a part is faulty or not.
(a) Turn the power switch off.
(b) Connect the Techstream to the DLC3.
(c) Turn the power switch on (IG).
(d) Turn the Techstream on.
(e) Enter the following menus: Chassis / Electric Parking Brake / Data List.
(f) Read the Data List according to the display on the Techstream.
Chassis > Electric Parking Brake > Data List
Tester Display | Measurement Item |
Range | Normal Condition |
Diagnostic Note |
Number of Trouble Codes |
Number of DTCs stored | 0 to 255 |
0 | - |
FR Speed Sensor Open | Front speed sensor RH open detection |
Normal or Error | Normal |
- |
FL Speed Sensor Open |
Front speed sensor LH open detection |
Normal or Error | Normal |
- |
RR Speed Sensor Open |
Rear speed sensor RH open detection |
Normal or Error | Normal |
- |
RL Speed Sensor Open |
Rear speed sensor LH open detection |
Normal or Error | Normal |
- |
EFI ECU Communication Open |
ECM communication open detection |
Normal or Error | Normal |
- |
Deceleration Sensor Open |
Deceleration sensor (airbag ECU assembly) communication open detection |
Normal or Error | Normal |
- |
HV ECU Communication Open |
Hybrid vehicle control ECU communication open detection |
Normal or Error | Normal |
- |
Body ECU Communication Open |
Main body ECU (multiplex network body ECU) communication open detection |
Normal or Error | Normal |
- |
Brake ECU Communication Open |
Skid control ECU (brake booster with master cylinder assembly) communication open detection |
Normal or Error | Normal |
- |
A/C ECU Communication Open |
Air conditioning amplifier assembly communication open detection |
Normal or Error | Normal |
- |
Navigation ECU Communication Open |
Radio receiver assembly communication open detection |
Normal or Error | Normal |
- |
Stop and Start ECU Communication Open |
Engine stop and start ECU communication open detection |
Normal or Error | Normal |
This item is displayed on the Techstream but is not used |
Deceleration Sensor Open (EPB) |
Deceleration sensor (airbag ECU assembly) communication open detection |
Normal or Error | Normal |
HINT: EPB stands for electric parking brake. |
FR Wheel Speed | Front wheel speed sensor RH reading |
0.0 to 326.4 km/h (0.0 to 202.8 mph) |
When vehicle is stopped: 0.0 km/h (0.0 mph) When
driving vehicle: Changes according to vehicle speed (when vehicle speed
is constant, there are no big changes in vehicle speed display) |
When not normal, front speed sensor RH system and CAN communication may be malfunctioning |
FL Wheel Speed | Front wheel speed sensor LH reading |
0.0 to 326.4 km/h (0.0 to 202.8 mph) |
When vehicle is stopped: 0.0 km/h (0.0 mph) When
driving vehicle: Changes according to vehicle speed (when vehicle speed
is constant, there are no big changes in vehicle speed display) |
When not normal, front speed sensor LH system and CAN communication may be malfunctioning |
RR Wheel Speed | Rear wheel speed sensor RH reading |
0.0 to 326.4 km/h (0.0 to 202.8 mph) |
When vehicle is stopped: 0.0 km/h (0.0 mph) When
driving vehicle: Changes according to vehicle speed (when vehicle speed
is constant, there are no big changes in vehicle speed display) |
When not normal, rear speed sensor RH system and CAN communication may be malfunctioning |
RL Wheel Speed | Rear wheel speed sensor LH reading |
0.0 to 326.4 km/h (0.0 to 202.8 mph) |
When vehicle is stopped: 0.0 km/h (0.0 mph) When
driving vehicle: Changes according to vehicle speed (when vehicle speed
is constant, there are no big changes in vehicle speed display) |
When not normal, rear speed sensor LH system and CAN communication may be malfunctioning |
Deceleration Sensor 1 | Deceleration sensor (airbag ECU assembly) 1 input signal |
-18.300 to 18.318 m/s2 |
When vehicle is stopped: 0.000 m/s2 When driving vehicle: Continuously changes |
When not normal, deceleration sensor (airbag ECU assembly) system and CAN communication may be malfunctioning |
Deceleration Sensor 2 | Deceleration sensor (airbag ECU assembly) 2 input signal |
-18.300 to 18.318 m/s2 |
When vehicle is stopped: 0.000 m/s2 When driving vehicle: Continuously changes |
When not normal, deceleration sensor (airbag ECU assembly) system and CAN communication may be malfunctioning |
Forward and Rearward G |
Deceleration sensor (airbag ECU assembly) input signal |
-18.300 to 18.318 m/s2 |
When vehicle is stopped: 0.000 m/s2 When driving vehicle: Changes according to increase or decrease in speed |
When not normal, deceleration sensor (airbag ECU assembly) system and CAN communication may be malfunctioning |
Zero Point of Deceleration Sensor |
Deceleration sensor (airbag ECU assembly) zero point |
-4.595 to 4.559 m/s2 |
- | - |
Zero Point of Deceleration Sensor 2 |
Deceleration sensor (airbag ECU assembly) 2 zero point |
-4.595 to 4.559 m/s2 |
- | - |
Vehicle Speed | Vehicle speed |
0.0 to 326.4 km/h (0.0 to 202.8 mph) |
When vehicle is stopped: 0.0 km/h (0.0 mph) When
driving vehicle: Changes according to vehicle speed (when vehicle speed
is constant, there are no big changes in vehicle speed display) |
When not normal, speed sensor system and CAN communication may be malfunctioning |
ECU +B1 Voltage | Skid control ECU (brake booster with master cylinder assembly) +B1 voltage |
0.00 to 20.00 V | 11 to 14 V |
- |
ECU +B2 Voltage |
Skid control ECU (brake booster with master cylinder assembly) +B2 voltage |
0.00 to 20.00 V | 11 to 14 V |
- |
RH Actuator Motor +Terminal Voltage |
Parking brake motor RH (parking brake actuator assembly RH) positive (+) terminal side voltage |
0.00 to 20.00 V | - |
- |
RH Actuator Motor -Terminal Voltage |
Parking brake motor RH (parking brake actuator assembly RH) negative (-) terminal side voltage |
0.00 to 20.00 V | - |
- |
LH Actuator Motor +Terminal Voltage |
Parking brake motor LH (parking brake actuator assembly LH) positive (+) terminal side voltage |
0.00 to 20.00 V | - |
- |
LH Actuator Motor -Terminal Voltage |
Parking brake motor LH (parking brake actuator assembly LH) negative (-) terminal side voltage |
0.00 to 20.00 V | - |
- |
Indoor Temperature |
Interior temperature | -6.50 to 57.25°C (20.3 to 135°F) |
- | When
displayed value differs from actual interior temperature, air
conditioning system and CAN communication system may be malfunctioning |
Ambient Temperature | Ambient temperature |
-40 to 50°C (-40 to 122°F) |
- | When
displayed value differs from actual ambient temperature, air
conditioning system and CAN communication system may be malfunctioning |
Stop Light Switch | Stop light switch assembly input signal |
OFF or ON | OFF: Brake pedal released
ON: Brake pedal depressed |
- |
EPB Switch |
Electric parking brake switch (electric parking brake switch assembly) input |
OFF, Lock, Release or Unknown |
OFF: Lock switch and release switch are off Lock: Lock switch on
Release: Release switch on |
When
not normal, electric parking brake switch (electric parking brake
switch assembly) release side system may be malfunctioning HINT: EPB stands for electric parking brake. |
Auto Mode Request | Auto mode request status |
OFF or ON | - |
- |
Shift Position |
Position of shift lever |
P, N, R, D or Unknown | P: Shift lever in P
N: Shift lever in N R: Shift lever in R D: Shift lever in D or S |
When not normal, shift position signal system may be malfunctioning |
IG Switch | IG power source status |
OFF or ON | OFF: IG power source voltage is not input to skid control ECU (brake booster with master cylinder assembly)
ON: IG power source voltage is input to skid control ECU (brake booster with master cylinder assembly) |
- |
Brake Hold Ready |
Brake hold control permission status |
OFF or ON | - |
- |
Brake Hold Control Mode |
Brake hold control mode |
OFF, ON, Release or EPB |
OFF: Brake hold control is not operating ON: Brake hold control is operating
Release: Brake hold control is released EPB: Parking brake is locked during brake hold control |
HINT: EPB stands for electric parking brake. |
EPB Lock Request | Lock demand status |
OFF or ON | OFF: Not requested
ON: Requested | HINT:
EPB stands for electric parking brake. |
FR Speed Signal Status |
FR speed signal status |
Normal or Stuck | Normal |
- |
FL Speed Signal Status |
FL speed signal status |
Normal or Stuck | Normal |
- |
RR Speed Signal Status |
RR speed signal status |
Normal or Stuck | Normal |
- |
RL Speed Signal Status |
RL speed signal status |
Normal or Stuck | Normal |
- |
RH Actuator Current Status |
Parking brake actuator assembly RH monitoring current condition |
Valid or Inval | Valid |
- |
LH Actuator Current Status |
Parking brake actuator assembly LH monitoring current condition |
Valid or Inval | Valid |
- |
RH Actuator Nut Stroke |
Parking brake actuator assembly RH nut stroke value |
0.000 to 8.160 mm (0.000 to 0.321 in.) |
- | - |
LH Actuator Nut Stroke |
Parking brake actuator assembly LH nut stroke value |
0.000 to 8.160 mm (0.000 to 0.321 in.) |
- | - |
RH Actuator Motor Actual Current |
Parking brake motor RH (parking brake actuator assembly RH) current value |
-5.0362 to 50.5000 A |
- | - |
RH Actuator Motor Adjustment Current |
Parking brake motor RH (parking brake actuator assembly RH) current calibration value |
-6.9690 to 6.9140 A | - |
- |
RH Actuator 0 load Current |
Parking brake actuator assembly RH current value with no load |
-5.0362 to 50.5000 A |
- | - |
LH Actuator Motor Actual Current |
Parking brake motor LH (parking brake actuator assembly LH) current value |
-5.0362 to 50.5000 A |
- | - |
LH Actuator Motor Adjustment Current |
Parking brake motor LH (parking brake actuator assembly LH) current calibration value |
-6.9690 to 6.9140 A | - |
- |
LH Actuator 0 load Current |
Parking brake actuator assembly LH current value with no load |
-5.0362 to 50.5000 A |
- | - |
Counter of IG ON After EPB Control Cancel |
Number of times the power switch was turned on (IG) after EPB control was canceled |
0 to 255 Times | - |
HINT: EPB stands for electric parking brake. |
RH Actuator Status | Parking brake actuator assembly RH condition |
Default,
Lock, Lock Dynamic, Release, Lock Faulty, Unexpected, Lock Standby,
Release Standby, Lock Dynamic Standby, Release Dynamic Standby, Lock
Dynamic Faulty, Lock Standard Control, Lock Dynamic Control, Lock
Control for Prevention Loosen by High Temperature, Lock Control for
Prevention Slipping Down, Re-Lock Control by Switch, Recovery Lock
Control, Lock Control After Dynamic PKB, Release Standard Control,
Release Dynamic Control or Full Release Control |
- | - |
LH Actuator Status | Parking brake actuator assembly LH condition |
Default,
Lock, Lock Dynamic, Release, Lock Faulty, Unexpected, Lock Standby,
Release Standby, Lock Dynamic Standby, Release Dynamic Standby, Lock
Dynamic Faulty, Lock Standard Control, Lock Dynamic Control, Lock
Control for Prevention Loosen by High Temperature, Lock Control for
Prevention Slipping Down, Re-Lock Control by Switch, Recovery Lock
Control, Lock Control After Dynamic PKB, Release Standard Control,
Release Dynamic Control or Full Release Control |
- | - |
RH Actuator Motor Current Differential |
Differences in parking brake motor RH (parking brake actuator assembly RH) monitoring current |
-1.008 to 0.945 A | - |
- |
LH Actuator Motor Current Differential |
Differences in parking brake motor LH (parking brake actuator assembly LH) monitoring current |
-1.008 to 0.945 A | - |
- |
Auto Mode |
AUTO (shift-linked) mode permission status |
OFF or ON | OFF: Manual mode
ON: AUTO (shift-linked) mode |
- |
Dynamic PKB Mode |
Dynamic parking brake operation status |
OFF or ON | OFF: Dynamic parking brake is not operating
ON: Dynamic parking brake is operating |
- |
Permission of Interlocking Shift |
AUTO (shift-linked) mode permission status |
OK or NG | - |
- |
Permission of Interlocking Brake |
Brake-linked permission status |
OK or NG | - |
- |
Permission of RH Interlocking PKB Lock |
Parking brake actuator assembly RH parking brake lock control permission status |
OK or NG | OK |
- |
Permission of RH Interlocking PKB Release |
Parking brake actuator assembly RH parking brake release control permission status |
OK or NG | - |
- |
Permission of RH Interlocking Dynamic PKB |
Parking brake actuator assembly RH dynamic parking control permission status |
OK or NG | - |
- |
Permission of RH Interlocking PKB Full Release |
Parking brake actuator assembly RH parking brake full release permission status |
OK or NG | - |
- |
Permission of LH Interlocking PKB Lock |
Parking brake actuator assembly RH parking brake lock control permission status |
OK or NG | OK |
- |
Permission of LH Interlocking PKB Release |
Parking brake actuator assembly RH parking brake release control permission status |
OK or NG | - |
- |
Permission of LH Interlocking Dynamic PKB |
Parking brake actuator assembly RH dynamic parking control permission status |
OK or NG | - |
- |
Permission of LH Interlocking PKB Full Release |
Parking brake actuator assembly LH parking brake full release permission status |
OK or NG | - |
- |
Fade Status |
Fade status | OFF or ON |
- | - |
EPB Control Cancel History |
Cause of EPB control cancel |
No
Recoded, RH IC Overheat, LH IC Overheat, RH Actuator Motor Current
High, LH Actuator Motor Current High, RH Actuator Motor +B Open Judging,
LH Actuator Motor +B Open Judging or IG Voltage High/Low |
- | HINT: EPB stands for electric parking brake. |
Parking Brake Light | Parking brake indicator light (red) output signal |
OFF, Light or Blink | OFF: Parking brake indicator light (red) turns off
Light: Parking brake indicator light (red) illuminates Blink: Parking brake indicator light (red) flashes |
- |
EPB Warning Light |
Brake system warning light (yellow indicator) output signal |
OFF or ON | OFF: Brake system warning light (yellow indicator) turns off
ON: Brake system warning light (yellow indicator) illuminates |
- |
AUTO Indicator |
AUTO indicator light output signal |
OFF or ON | - |
This item is displayed on the Techstream, however, it is not used for this vehicle |
PERFORM ACTIVE TEST
HINT:
Using
the Techstream to perform Active Tests allows relays, VSVs, actuators
and other items to be operated without removing any parts. This
non-intrusive functional inspection can be very useful because
intermittent operation may be discovered before parts or wiring is
disturbed. Performing Active Tests early in troubleshooting is one way
to save diagnostic time. Data List information can be displayed while
performing Active Tests.
(a) Turn the power switch off.
(b) Connect the Techstream to the DLC3.
(c) Turn the power switch on (IG).
(d) Turn the Techstream on.
(e) Enter the following menus: Chassis / Electric Parking Brake / Active Test.
(f) According to the display on the Techstream, perform the Active Test.
Chassis > Electric Parking Brake > Active Test
Tester Display | Measurement Item |
Control Range | Diagnostic Note |
Auto Mode | AUTO (shift-linked) mode |
ON or OFF |
- Vehicle stopped
- Power switch on (IG)
|
EPB Warning Light |
Brake system warning light (yellow) |
ON or OFF |
- Vehicle stopped
- Power switch on (IG)
HINT: EPB stands for electric parking brake. |
PKB Light | Parking brake indicator light (red) |
ON or OFF |
- Vehicle stopped
- Power switch on (IG)
|
PKB Lock Control |
Parking brake lock control |
ON or OFF |
- Vehicle stopped
- Power switch on (IG)
|
PKB Release Control |
Parking brake release control |
ON or OFF |
- Vehicle stopped
- Power switch on (IG)
|
PKB Full Release Control |
Parking brake full release control |
ON or OFF |
- Vehicle stopped
- Power switch on (IG)
|
Diagnostic Trouble Code Chart
DIAGNOSTIC TROUBLE CODE CHART
Electric Parking Brake System
DTC No. | Detection Item |
Memory | Note |
Link |
C1245 |
Deceleration Sensor | DTC stored |
An electric parking brake system malfunction is displayed on the multi-information display. |
|
C13A0 | Open circuit in Power source circuit |
DTC stored | An electric parking brake system malfunction is displayed on the multi-information display. |
|
C13A1 | Short circuit in Power source circuit |
DTC stored | An electric parking brake system malfunction is displayed on the multi-information display. |
|
C13A2 | Engine Switch/Power Switch Malfunction |
DTC stored | An electric parking brake system malfunction is displayed on the multi-information display. |
|
C13A5 | Electric Current of Motor |
DTC stored | An electric parking brake system malfunction is displayed on the multi-information display. |
|
C13A6 | Open or Short Circuit in Motor |
DTC stored | An electric parking brake system malfunction is displayed on the multi-information display. |
|
C13A7 | Actuator Malfunction |
DTC stored | An electric parking brake system malfunction is displayed on the multi-information display. |
|
C13A9 | Brake System Malfunction |
DTC stored | An electric parking brake system malfunction is displayed on the multi-information display. |
|
C13AA | EPB High Temperature |
DTC stored | A
warning is displayed on the multi-information display indicating
electric parking brake system operation is stopped due to high
temperatures. |
|
C13AE | System information not received |
DTC stored | An electric parking brake system malfunction is displayed on the multi-information display. |
|
C13B0 | Electric Parking Brake ECU Malfunction |
DTC stored | An electric parking brake system malfunction is displayed on the multi-information display. |
|
C13B4 | EPB Switch Malfunction |
DTC stored | An electric parking brake system malfunction is displayed on the multi-information display. |
|
U0073 | Control Module Communication Bus OFF |
DTC stored | An electric parking brake system malfunction is displayed on the multi-information display. |
|
U0100 | Lost Communication With ECM/PCM "A" |
DTC stored | An electric parking brake system malfunction is displayed on the multi-information display. |
|
U0124 | Lost Communication With Lateral Acceleration Sensor Module |
DTC stored | An electric parking brake system malfunction is displayed on the multi-information display. |
|
U0129 | Lost Communication with Brake System Control Module |
DTC stored | An electric parking brake system malfunction is displayed on the multi-information display. |
|
U0293 | Lost Communication With Hybrid Vehicle Control System |
DTC stored | An electric parking brake system malfunction is displayed on the multi-information display. |
|
Dtc Check / Clear
DTC CHECK / CLEAR
CHECK DTC AND FREEZE FRAME DATA (USING TECHSTREAM)
(a) Turn the power switch off.
(b) Connect the Techstream to the DLC3.
(c) Turn the power switch on (IG).
(d) Turn the Techstream on.
(e) Enter the following menus: Chassis / Electric Parking Brake / Trouble Codes.
Chassis > Electric Parking Brake > Trouble Codes
(f) Check for DTCs.
(g) Check the freeze frame data.
- If DTCs are output, check the freeze frame data and read the vehicle status when the DTC was stored.
HINT:
for Freeze Frame Data: Click here
CLEAR DTC AND FREEZE FRAME DATA (USING TECHSTREAM)
(a) Turn the power switch off.
(b) Connect the Techstream to the DLC3.
(c) Turn the power switch on (IG).
(d) Turn the Techstream on.
(e) Enter the following menus: Chassis / Electric Parking Brake / Trouble Codes.
(f) Clear the DTCs.
Chassis > Electric Parking Brake > Clear DTCs
HINT:
When DTCs are cleared, the freeze frame data will also be cleared.
Electric Parking Brake does not Operate
WIRING DIAGRAM
CAUTION / NOTICE / HINT
NOTICE:
- Inspect the fuses for circuits related to this system before performing the following procedure.
- The electric parking brake may still operate up to 20 seconds after the
power switch is turned off. Before disconnecting connectors or fuses,
turn the power switch off and wait 20 seconds or more.
- The parking brake indicator light blinks (red) when the power switch is
turned on (IG) after replacing the parking brake ECU (brake actuator
assembly). Operate the electric parking brake switch (electric parking
brake switch assembly) to turn off the parking brake indicator light
(red).
HINT:
Even if
the electric parking brake is operating normally, the parking brake
indicator light (red) on the combination meter may be malfunctioning.
PROCEDURE
1. |
CHECK CAN COMMUNICATION SYSTEM |
(a) Check if CAN communication system DTCs are output.
Click here
Result | Proceed to |
DTCs are not output | A |
DTCs are output | B |
B |
| GO TO CAN COMMUNICATION SYSTEM |
A |
| |
2. |
VEHICLE OPERATION CHECK |
(a)
When the vehicle's tires are lifted off the ground and the Techstream
is used to operate the electric parking brake, check the condition of
the rear tires.
Click here
Result | Proceed to |
Lock and release operation is normal and parking brake indicator light turns off or blinks (red) |
A |
Lock
and release operation is malfunctioning and parking brake indicator
light illuminates (red) or turns off according to switch operation |
B |
Lock and release operation is malfunctioning and parking brake indicator light turns off or blinks (red) |
C |
B |
| INSPECT REAR BRAKE |
C |
| GO TO STEP 5 |
A |
| |
3. |
PERFORM TECHSTREAM (PARKING BRAKE LIGHT) |
(a) Turn the power switch off.
(b) Connect the Techstream to the DLC3.
(c) Turn the power switch on (IG).
(d) Turn the Techstream on.
(e) Enter the following menus: Chassis / Electric Parking Brake / Active Test.
(f) Perform the Active Test according to the display on the Techstream.
Chassis > Electric Parking Brake > Active Test
Tester Display | Measurement Item |
Control Range | Diagnostic Note |
PKB Light | Parking brake indicator light (red) |
ON or OFF |
- Vehicle stopped
- Power switch on (IG)
|
Chassis > Electric Parking Brake > Active Test
(g) Select the Data List on the Techstream.
Chassis > Electric Parking Brake > Data List
Tester Display | Measurement Item |
Range | Normal Condition |
Diagnostic Note |
Parking Brake Light | Parking brake indicator light (red) output signal |
OFF, Light or Blink | OFF: Parking brake indicator light (red) turns off
Light: Parking brake indicator light (red) illuminates Blink: Parking brake indicator light (red) flashes |
- |
Chassis > Electric Parking Brake > Data List
Tester Display |
Parking Brake Light |
(h) Check the operating condition of the parking brake indicator light (red) when operating it using the Techstream.
Result | Proceed to |
The value of the Data List item does not change in accordance with the Active Test |
A |
The value of the Data List item changes in accordance with the Active Test |
B |
A |
| REPLACE PARKING BRAKE ECU (BRAKE ACTUATOR ASSEMBLY) |
B |
| |
4. |
INSPECT COMBINATION METER ASSEMBLY |
(a) Perform the Active Test of the combination meter assembly using the Techstream.
Body Electrical > Combination Meter > Active Test
Tester Display |
Indicat. Park |
(b) Check the combination meter assembly.
OK:
Parking brake indicator light (red) turns on or off in accordance with Techstream operation.
OK |
| REPLACE PARKING BRAKE ECU (BRAKE ACTUATOR ASSEMBLY) |
NG |
| GO TO METER / GAUGE SYSTEM |
5. |
CHECK HARNESS AND CONNECTOR (BEPB CIRCUIT) |
*a | Front view of wire harness connector (to Parking Brake ECU (Brake Actuator Assembly)) |
(a) Turn the power switch off.
(b) Disconnect the A39 parking brake ECU (brake actuator assembly) connector.
(c) Measure the voltage according to the value(s) in the table below.
Standard Voltage:
Tester Connection | Condition |
Specified Condition |
A39-9 (BEPB) - Body ground |
Power switch off | 11 to 14 V |
NG |
| REPAIR OR REPLACE HARNESS OR CONNECTOR |
OK |
| |
6. |
CHECK HARNESS AND CONNECTOR (AUXILIARY BATTERY - PARKING BRAKE ECU (BRAKE ACTUATOR ASSEMBLY)) |
*a | Front view of wire harness connector (to Parking Brake ECU (Brake Actuator Assembly)) |
(a) Turn the power switch off.
(b) Disconnect the A39 parking brake ECU (brake actuator assembly) connector.
(c) Measure the voltage according to the value(s) in the table below.
Standard Voltage:
Tester Connection | Condition |
Specified Condition |
A39-26 (IG) - Body ground |
Power switch on (IG) |
8 to 16 V |
OK |
| REPLACE PARKING BRAKE ECU (BRAKE ACTUATOR ASSEMBLY) |
NG |
| REPAIR OR REPLACE HARNESS OR CONNECTOR |
Electric Parking Brake System AUTO Function Circuit
DESCRIPTION
The parking
brake ECU (brake actuator assembly) receives shift position information
from the hybrid vehicle control ECU via CAN communication, and wheel
speed signal and stop light switch signals from the skid control ECU
(brake booster with master cylinder assembly).
The
electric parking brake system AUTO function (shift-linked function)
automatically releases the parking brake when the following conditions
are met: 1) Power switch is on (IG), 2) brake pedal is depressed, and 3)
shift lever is moved out of P. When the shift lever is moved to P with
these conditions met, the function automatically locks the parking
brake.
The electric parking brake system AUTO
(shift-linked function) automatically engages the parking brake when the
shift lever is moved to P and disengages the parking brake when the
shift lever is moved out of P when the power switch is on (IG) and the
brake pedal is depressed.
WIRING DIAGRAM
CAUTION / NOTICE / HINT
NOTICE:
The
parking brake indicator light blinks (red) when the power switch is
turned on (IG) after replacing the parking brake ECU (brake actuator
assembly). Operate the electric parking brake switch (electric parking
brake switch assembly) to turn off the parking brake indicator light
(red).
PROCEDURE
1. | CHECK DTC (ELECTRONICALLY CONTROLLED BRAKE SYSTEM) |
(a) Check for DTCs.
Chassis > ABS/VSC/TRAC > Trouble Codes
Result | Proceed to |
DTC is not output | A |
DTC is output | B |
B |
| GO TO ELECTRONICALLY CONTROLLED BRAKE SYSTEM |
A |
| |
2. |
CHECK DTC (HYBRID CONTROL SYSTEM) |
(a) Check for DTCs.
Powertrain > Hybrid Control > Trouble Codes
Result | Proceed to |
DTC is not output | A |
DTC is output | B |
A |
| REPLACE PARKING BRAKE ECU (BRAKE ACTUATOR ASSEMBLY) |
B |
| GO TO HYBRID CONTROL SYSTEM |
Fail-safe Chart
FAIL-SAFE CHART
DTC | Trouble Area |
Brake System Warning Light (Yellow) |
Parking Brake Indicator Light (Red) |
Fail-safe Deactivation Condition |
C1245 | Deceleration sensor data malfunction |
Illuminates | Normal |
20 seconds after power switch turned off |
C13A0 | Open in power supply relay circuit |
Illuminates | Normal* |
20 seconds after power switch turned off |
C13A1 | Short in power supply relay circuit |
Illuminates | Normal |
20 seconds after power switch turned off |
C13A2 | Power switch malfunction |
Illuminates | Normal |
20 seconds after power switch turned off |
C13A5 | Parking brake motor (Parking brake actuator assembly) current monitor malfunction |
Illuminates | Normal* |
20 seconds after power switch turned off |
C13A6 | Parking brake motor (Parking brake actuator assembly) open or short malfunction |
Illuminates | Normal* |
20 seconds after power switch turned off |
C13A7 | Parking brake actuator assembly malfunction (jamming, spinning, repeated slipping) |
Illuminates | Normal* |
Parking brake actuator assembly normal |
C13A9 | Brake Control System Malfunction |
Illuminates | Normal |
Wheel speed of 1 wheel or more received normally |
C13AA | Electric parking brake high temperature |
Does not illuminate | Blinks |
Wait 1 minute |
C13AE | System information not received malfunction |
Illuminates | Normal |
System information received |
C13B0 | ECU malfunction |
Illuminates | Normal* |
Parking brake ECU (brake actuator assembly) normal |
C13B4 | Electric parking brake switch open or short circuit malfunction |
Illuminates | Blinks |
After returning to normal condition, turn power switch again |
U0073 | CAN communication system malfunction |
Illuminates | Normal |
Power switch off |
U0100 | SFI system communication malfunction |
Illuminates | Normal |
Communication normal, power switch off |
U0124 | Deceleration sensor communication malfunction |
Illuminates | Normal |
Communication normal, power switch off |
U0129 | Brake system communication malfunction |
Illuminates | Normal |
Communication normal, power switch off |
U0293 | Hybrid vehicle control ECU communication malfunction |
Illuminates | Normal |
Communication normal, power switch off |
- *: The parking brake indicator light blinks (red) if the electric parking brake switch assembly is pulled or pushed.
Freeze Frame Data
FREEZE FRAME DATA
FREEZE FRAME DATA
HINT:
- When a DTC is stored, the freeze frame data stores the current vehicle (sensor) state as.
- The freeze frame data cannot be cleared or updated until the recorded DTCs are cleared.
(a) Using the Techstream, the state
of the vehicle (sensors) when the system is operating or when a DTC was
stored can be checked.
Chassis > Electric Parking Brake
Tester Display | Measurement Item |
Range | Normal Condition |
Diagnostic Note |
FR Speed Sensor Open | Front speed sensor RH open detection |
Normal or Error | Normal |
- |
FL Speed Sensor Open |
Front speed sensor LH open detection |
Normal or Error | Normal |
- |
RR Speed Sensor Open |
Rear speed sensor RH open detection |
Normal or Error | Normal |
- |
RL Speed Sensor Open |
Rear speed sensor LH open detection |
Normal or Error | Normal |
- |
EFI ECU Communication Open |
ECM communication open detection |
Normal or Error | Normal |
- |
Deceleration Sensor Open |
Deceleration sensor (airbag ECU assembly) communication open detection |
Normal or Error | Normal |
- |
HV ECU Communication Open |
Hybrid vehicle control ECU communication open detection |
Normal or Error | Normal |
- |
Body ECU Communication Open |
Main body ECU (multiplex network body ECU) communication open detection |
Normal or Error | Normal |
- |
Brake ECU Communication Open |
Skid control ECU (brake booster with master cylinder assembly) communication open detection |
Normal or Error | Normal |
- |
A/C ECU Communication Open |
Air conditioning amplifier assembly communication open detection |
Normal or Error | Normal |
- |
Navigation ECU Communication Open |
Radio receiver assembly communication open detection |
Normal or Error | Normal |
- |
Stop and Start ECU Communication Open |
Engine stop and start ECU communication open detection |
Normal or Error | Normal |
- |
Deceleration Sensor Open (EPB) |
Acceleration sensor open detection |
Normal or Error | Normal |
HINT: EPB stands for electric parking brake. |
FR Wheel Speed | Front wheel speed sensor RH reading |
0.0 to 326.4 km/h (0 to 202 mph) |
When vehicle is stopped: 0 km/h (0 mph) When
driving vehicle: Changes according to vehicle speed (when vehicle speed
is constant, there are no big changes in vehicle speed display) |
When not normal, front speed sensor RH system and CAN communication may be malfunctioning |
FL Wheel Speed | Front wheel speed sensor LH reading |
0.0 to 326.4 km/h (0 to 202 mph) |
When vehicle is stopped: 0 km/h (0 mph) When
driving vehicle: Changes according to vehicle speed (when vehicle speed
is constant, there are no big changes in vehicle speed display) |
When not normal, front speed sensor LH system and CAN communication may be malfunctioning |
RR Wheel Speed | Rear wheel speed sensor RH reading |
0.0 to 326.4 km/h (0 to 202 mph) |
When vehicle is stopped: 0 km/h (0 mph) When
driving vehicle: Changes according to vehicle speed (when vehicle speed
is constant, there are no big changes in vehicle speed display) |
When not normal, rear speed sensor RH system and CAN communication may be malfunctioning |
RL Wheel Speed | Rear wheel speed sensor LH reading |
0.0 to 326.4 km/h (0 to 202 mph) |
When vehicle is stopped: 0 km/h (0 mph) When
driving vehicle: Changes according to vehicle speed (when vehicle speed
is constant, there are no big changes in vehicle speed display) |
When not normal, rear speed sensor LH system and CAN communication may be malfunctioning |
Deceleration Sensor 1 | Deceleration sensor (airbag ECU assembly) 1 input signal |
-18.300 to 18.318 m/s2 |
When vehicle is stopped: 0 m/s2 When driving vehicle: Continuously changes |
When not normal, deceleration sensor (airbag ECU assembly) system and CAN communication may be malfunctioning |
Deceleration Sensor 2 | Deceleration sensor (airbag ECU assembly) 2 input signal |
-18.300 to 18.318 m/s2 |
When vehicle is stopped: 0 m/s2 When driving vehicle: Continuously changes |
When not normal, deceleration sensor (airbag ECU assembly) system and CAN communication may be malfunctioning |
Forward and Rearward G |
Deceleration sensor (airbag ECU assembly) input signal |
-18.300 to 18.318 m/s2 |
When vehicle is stopped: 0 m/s2 When driving vehicle: Changes according to increase or decrease in speed |
When not normal, deceleration sensor (airbag ECU assembly) system and CAN communication may be malfunctioning |
Zero Point of Deceleration Sensor |
Deceleration sensor (airbag ECU assembly) zero point |
-4.595 to 4.559 m/s2 |
- | - |
Zero Point of Deceleration Sensor 2 |
Deceleration sensor (airbag ECU assembly) 2 zero point |
-4.595 to 4.559 m/s2 |
- | - |
Vehicle Speed | Vehicle speed |
0.0 to 326.4 km/h (0.0 to 202.8 mph) |
When vehicle is stopped: 0 km/h (0 mph) When
driving vehicle: Changes according to vehicle speed (when vehicle speed
is constant, there are no big changes in vehicle speed display) |
When not normal, speed sensor system and CAN communication may be malfunctioning |
ECU +B1 Voltage | Skid control ECU (brake booster with master cylinder assembly) +B1 voltage |
0.00 to 20.00 V | 11 to 14 V |
- |
ECU +B2 Voltage |
Skid control ECU (brake booster with master cylinder assembly) +B2 voltage |
0.00 to 20.00 V | 11 to 14 V |
- |
RH Actuator Motor +Terminal Voltage |
Parking brake motor RH (parking brake actuator assembly RH) positive (+) terminal side voltage |
0.00 to 20.00 V | - |
- |
RH Actuator Motor -Terminal Voltage |
Parking brake motor RH (parking brake actuator assembly RH) negative (-) terminal side voltage |
0.00 to 20.00 V | - |
- |
LH Actuator Motor +Terminal Voltage |
Parking brake motor LH (parking brake actuator assembly LH) positive (+) terminal side voltage |
0.00 to 20.00 V | - |
- |
LH Actuator Motor -Terminal Voltage |
Parking brake motor LH (parking brake actuator assembly LH) negative (-) terminal side voltage |
0.00 to 20.00 V | - |
- |
Stop Light Switch |
Stop light switch assembly |
OFF or ON | OFF: Brake pedal released
ON: Brake pedal depressed |
- |
EPB Switch |
Electric parking brake switch (electric parking brake switch assembly) input |
OFF, Lock, Release or Unknown |
OFF: Lock switch and release switch are off Lock: Lock switch on
Release: Release switch on |
When
not normal, electric parking brake switch (electric parking brake
switch assembly) release side system may be malfunctioning HINT: EPB stands for electric parking brake. |
Auto Mode Request | Auto mode request status |
OFF or ON | - |
- |
Shift Position |
Position of shift lever |
P, N, R, D or Unknown | P: Shift lever in P
N: Shift lever in N R: Shift lever in R D: Shift lever in D or S |
When not normal, shift position signal system may be malfunctioning |
IG Switch | IG power source status |
OFF or ON | OFF: IG power source voltage is not input to Parking brake ECU (brake actuator assembly)
ON: IG power source voltage is input to Parking brake ECU (brake actuator assembly) |
- |
Brake Hold Ready |
Brake hold control permission status |
OFF or ON | - |
- |
Brake Hold Control Mode |
Brake hold control mode |
OFF, ON, Release or EPB |
OFF: Brake hold control is not operating ON: Brake hold control is operating
Release: Brake hold control is released EPB: Parking brake is locked during brake hold control |
HINT: EPB stands for electric parking brake. |
EPB Lock Request | Lock demand status |
OFF or ON | OFF: Not requested
ON: Requested | HINT:
EPB stands for electric parking brake. |
FR Speed Signal Status |
FR speed signal status |
Normal or Stuck | Normal |
- |
FL Speed Signal Status |
FL speed signal status |
Normal or Stuck | Normal |
- |
RR Speed Signal Status |
RR speed signal status |
Normal or Stuck | Normal |
- |
RL Speed Signal Status |
RL speed signal status |
Normal or Stuck | Normal |
- |
RH Actuator Current Status |
Parking brake actuator assembly RH monitoring current condition |
Valid or Inval | Valid |
- |
LH Actuator Current Status |
Parking brake actuator assembly LH monitoring current condition |
Valid or Inval | Valid |
- |
RH Actuator Nut Stroke |
Parking brake actuator assembly RH nut stroke value |
0.000 to 8.160 mm (0.000 to 0.321 in.) |
- | - |
LH Actuator Nut Stroke |
Parking brake actuator assembly LH nut stroke value |
0.000 to 8.160 mm (0.000 to 0.321 in.) |
- | - |
RH Actuator Motor Actual Current |
Parking brake motor RH (parking brake actuator assembly RH) current value |
-5.0362 to 50.5000 A |
- | - |
RH Actuator Motor Adjustment Current |
Parking brake motor RH (parking brake actuator assembly RH) current calibration value |
-6.9690 to 6.9140 A | - |
- |
RH Actuator 0 load Current |
Parking brake actuator assembly RH current value with no load |
-5.0362 to 50.5000 A |
- | - |
LH Actuator Motor Actual Current |
Parking brake motor LH (parking brake actuator assembly LH) current value |
-5.0362 to 50.5000 A |
- | - |
LH Actuator Motor Adjustment Current |
Parking brake motor LH (parking brake actuator assembly LH) current calibration value |
-6.9690 to 6.9140 A | - |
- |
LH Actuator 0 load Current |
Parking brake actuator assembly LH current value with no load |
-5.0362 to 50.5000 A |
- | - |
Counter of IG ON After EPB Control Cancel |
Number of times the power switch was turned on (IG) after EPB control was canceled |
0 to 255 Times | - |
HINT: EPB stands for electric parking brake. |
RH Actuator Status | Parking brake actuator assembly RH condition |
Default,
Lock, Lock Dynamic, Release, Lock Faulty, Unexpected, Lock Standby,
Release Standby, Lock Dynamic Standby, Release Dynamic Standby, Lock
Dynamic Faulty, Lock Standard Control, Lock Dynamic Control, Lock
Control for Prevention Loosen by High Temperature, Lock Control for
Prevention Slipping Down, Re-Lock Control by Switch, Recovery Lock
Control, Lock Control After Dynamic PKB, Release Standard Control,
Release Dynamic Control or Full Release Control |
- | - |
LH Actuator Status | Parking brake actuator assembly LH condition |
Default,
Lock, Lock Dynamic, Release, Lock Faulty, Unexpected, Lock Standby,
Release Standby, Lock Dynamic Standby, Release Dynamic Standby, Lock
Dynamic Faulty, Lock Standard Control, Lock Dynamic Control, Lock
Control for Prevention Loosen by High Temperature, Lock Control for
Prevention Slipping Down, Re-Lock Control by Switch, Recovery Lock
Control, Lock Control After Dynamic PKB, Release Standard Control,
Release Dynamic Control or Full Release Control |
- | - |
RH Actuator Motor Current Differential |
Differences in parking brake motor RH (parking brake actuator assembly RH) monitoring current |
-1.008 to 0.945 A | - |
- |
LH Actuator Motor Current Differential |
Differences in parking brake motor LH (parking brake actuator assembly LH) monitoring current |
-1.008 to 0.945 A | - |
- |
Detailed Freeze DTC |
Number of detailed freeze DTCs |
0 to 65535 | - |
- |
RH Actuator Motor Gradient Current |
Parking brake motor RH (parking brake actuator assembly RH) current gradient |
-5.0362 to 50.5000 A |
- | - |
LH Actuator Motor Gradient Current |
Parking brake motor LH (parking brake actuator assembly LH) current gradient |
-5.0362 to 50.5000 A |
- | - |
RH Actuator Motor Relay1 |
Parking brake motor relay 1 RH condition |
OFF or ON | - |
- |
RH Actuator Motor Relay2 |
Parking brake motor relay 2 RH condition |
OFF or ON | - |
- |
RH Actuator Motor Relay3 |
Parking brake motor relay 3 RH condition |
OFF or ON | - |
- |
RH Actuator Motor Relay4 |
Parking brake motor relay 4 RH condition |
OFF or ON | - |
- |
LH Actuator Motor Relay1 |
Parking brake motor relay 1 LH condition |
OFF or ON | - |
- |
LH Actuator Motor Relay2 |
Parking brake motor relay 2 LH condition |
OFF or ON | - |
- |
LH Actuator Motor Relay3 |
Parking brake motor relay 3 LH condition |
OFF or ON | - |
- |
LH Actuator Motor Relay4 |
Parking brake motor relay 4 LH condition |
OFF or ON | - |
- |
RH Actuator Motor Current High |
Parking brake motor RH (parking brake actuator assembly RH) overcurrent |
OFF or ON | - |
- |
RH Actuator Motor Driver Operation Status |
Parking brake motor RH (parking brake actuator assembly RH) driver status |
OK or NG | - |
- |
LH Actuator Motor Current High |
Parking brake motor LH (parking brake actuator assembly LH) overcurrent status |
OFF or ON | - |
- |
LH Actuator Motor Driver Operation Status |
Parking brake motor LH (parking brake actuator assembly LH) driver status |
OK or NG | - |
- |
How To Proceed With Troubleshooting
CAUTION / NOTICE / HINT
HINT:
*: Use the Techstream.
PROCEDURE
1. |
VEHICLE BROUGHT TO WORKSHOP |
NEXT |
| |
2. |
CUSTOMER PROBLEM ANALYSIS |
(a) Interview the customer and confirm the problem.
Click here
NEXT |
| |
3. |
INSPECT AUXILIARY BATTERY VOLTAGE |
Standard Voltage:
11 to 14 V
- If the voltage is below 11 V, recharge or replace the auxiliary battery before proceeding to the next step.
NEXT |
| |
4. |
CHECK DTC AND FREEZE FRAME DATA* |
(a) Check and record DTCs and freeze frame data.
Chassis > Electric Parking Brake > Trouble Codes
(b) Clear the DTCs and freeze frame data.
Chassis > Electric Parking Brake > Clear DTCs
(c) Recheck for DTCs.
(1) Reconfirm the DTCs based on the recorded DTCs and freeze frame data.
Chassis > Electric Parking Brake > Trouble Codes
(2)
Try to reproduce the problem symptoms based on the recorded DTCs and
freeze frame data, and then check if the DTCs are output again.
Result |
Proceed to |
DTCs are not output (Problem symptom occurs.) |
A |
DTCs are output |
B |
DTCs are not output (Problem symptom does not occur.) |
C |
HINT:
- Refer to Diagnostic Trouble Code Chart if any DTCs are output.
- When DTCs indicating a CAN communication system malfunction are output,
first troubleshoot and repair the CAN communication system.
B |
| GO TO DIAGNOSTIC TROUBLE CODE CHART |
C |
| USE SIMULATION METHOD TO CHECK |
A |
| |
5. |
PROBLEM SYMPTOMS TABLE |
(a) Proceed to Problem Symptoms Table.
Click here
Result |
Proceed to |
Fault is not listed in Problem Symptoms Table |
A |
Fault is listed in Problem Symptoms Table |
B |
B |
| GO TO STEP 7 |
A |
| |
6. |
OVERALL ANALYSIS AND TROUBLESHOOTING* |
(a) Refer to Terminals of ECU.
Click here
(b) Refer to Data List / Active Test.
Click here
NEXT |
| |
NEXT |
| |
NEXT |
| END |
Message Not Displayed on Multi-information Display When AUTO Function Set to ON/OFF
DESCRIPTION
When the AUTO
function is set to ON/OFF, a message is displayed on the
multi-information display in the combination meter assembly.
WIRING DIAGRAM
PROCEDURE
1. |
CHECK OPERATION OF AUTO FUNCTION |
(a) Check that the AUTO function operates when the operating conditions are met.
HINT:
Do not use the multi-information display to determine whether the AUTO function is operating or not.
Result |
Proceed to |
The AUTO function operates |
A |
The AUTO function does not operate |
B |
A |
| REPLACE COMBINATION METER ASSEMBLY |
B |
| GO TO Electric Parking Brake System AUTO Function Circuit |
Parts Location
PARTS LOCATION
ILLUSTRATION
*1 | PARKING BRAKE ECU (BRAKE ACTUATOR ASSEMBLY) |
*2 | ECM |
*3 | NO. 1 ENGINE ROOM RELAY BLOCK AND NO. 1 JUNCTION BLOCK ASSEMBLY
- EPB NO. 1 FUSE | *4 |
SKID CONTROL ECU ASSEMBLY (BRAKE BOOSTER WITH MASTER CYLINDER ASSEMBLY) |
ILLUSTRATION
*1 | PARKING BRAKE ACTUATOR ASSEMBLY LH |
*2 | PARKING BRAKE ACTUATOR ASSEMBLY RH |
*3 | ELECTRIC PARKING BRAKE SWITCH (ELECTRIC PARKING BRAKE SWITCH ASSEMBLY) |
*4 | MAIN BODY ECU (MULTIPLEX NETWORK BODY ECU) |
*5 | HYBRID VEHICLE CONTROL ECU |
*6 | COMBINATION METER ASSEMBLY |
*7 | RADIO RECEIVER ASSEMBLY |
*8 | INSTRUMENT PANEL JUNCTION BLOCK ASSEMBLY
- ECU-IG1 NO. 3 FUSE - ECU-B NO. 2 FUSE |
*9 | DLC3 |
*10 | AIR CONDITIONING AMPLIFIER ASSEMBLY |
*11 | DECELERATION SENSOR (AIRBAG ECU ASSEMBLY) |
*12 | NO. 2 PARKING BRAKE WIRE ASSEMBLY |
*13 | NO. 1 PARKING BRAKE WIRE ASSEMBLY |
- | - |
Precaution
PRECAUTION
PRECAUTION FOR DISCONNECTING CABLE FROM NEGATIVE AUXILIARY BATTERY TERMINAL
NOTICE:
When
disconnecting the cable from the negative (-) auxiliary battery
terminal, initialize the following system(s) after the cable is
reconnected.
System | See Procedure |
Lane Departure Alert System (w/ Steering Control) |
|
Intelligent Clearance Sonar System |
Parking Assist Monitor System |
Panoramic View Monitor System |
Pre-collision System |
Lighting System (for HV Model with Cornering Light) |
TROUBLESHOOTING PRECAUTIONS
(a)
When inspecting the rear brakes, disconnect the connector of the
parking brake actuator assembly or disconnect the cable from the
negative (-) auxiliary battery terminal.
CAUTION:
- Do not perform the rear brake inspection while either the parking brake
actuator assembly connector or the negative (-) auxiliary battery
terminal are connected.
- The rear disc brake piston could operate, resulting in an accident such as hands being caught.
(b) The electric parking brake may
still operate up to 20 seconds after the power switch is turned off.
Before disconnecting connectors or fuses, turn the power switch off and
wait 20 seconds or more.
(c) If a component has
been removed and installed, confirm that the system operates normally by
checking for DTCs after installation has been completed.
HANDLING PRECAUTIONS
(a)
When tilting the vehicle to perform work after parking the vehicle on a
level surface, the braking force may not be sufficient. Make sure to
pull the electric parking brake switch (electric parking brake switch
assembly) to the lock side 2 times (2 lock operations).
HINT:
- The electric parking brake system determines the amount of force used to
operate the parking brake according to the tilt angle detected by the
deceleration sensor (airbag ECU assembly).
- When the parking brake indicator (red) is illuminated after the electric
parking brake switch (electric parking brake switch assembly) has been
pulled to the lock side, the maximum amount of braking force is applied
if the electric parking brake switch (electric parking brake switch
assembly) is pulled to the lock side one more time.
(b) The parking brake indicator
light blinks (red) when the power switch is turned on (IG) after
replacing the parking brake ECU (brake actuator assembly). Operate the
electric parking brake switch (electric parking brake switch assembly)
to turn off the parking brake indicator light (red).
PRECAUTIONS FOR TOWING VEHICLES
(a) For towing precautions: Click here
PARKING BRAKE FORCED RELEASE METHOD
(a) For the parking brake forced release method: Click here
Problem Symptoms Table
PROBLEM SYMPTOMS TABLE
HINT:
- Use the table below to help determine the cause of problem symptoms. If
multiple suspected areas are listed, the potential causes of the
symptoms are listed in order of probability in the "Suspected Area"
column of the table. Check each symptom by checking the suspected areas
in the order they are listed. Replace parts as necessary.
- Inspect the fuses and relays related to this system before inspecting the suspected areas below.
Symptom | Suspected Area |
Link |
Electric parking brake does not operate |
Proceed to "Electric Parking Brake does not Operate" |
|
Parking brake indicator light does not illuminate (red) or turn off when parking brake is manually engaged and disengaged |
Proceed to "Electric Parking Brake does not Operate" |
|
Electric
parking brake AUTO function (shift-linked function) does not operate
(shift-linked parking brake does not lock or release) |
Proceed to "Electric Parking Brake System AUTO Function Circuit" |
|
Message not displayed on multi-information display when AUTO function set to ON/OFF |
Proceed to "Message Not Displayed on Multi-Information Display When AUTO Function Set to ON/OFF" |
|
Electric
parking brake switch indicator light on electric parking brake switch
(electric parking brake switch assembly) does not illuminate or turn off
when lock and release operations are performed |
Electric parking brake switch indicator light drive circuit |
|
Wire harness or connector (electric parking brake switch assembly - parking brake ECU (brake actuator assembly)) |
- |
Electric parking brake switch (electric parking brake switch assembly) |
|
Parking brake ECU (brake actuator assembly) |
|
System Diagram
SYSTEM DIAGRAM
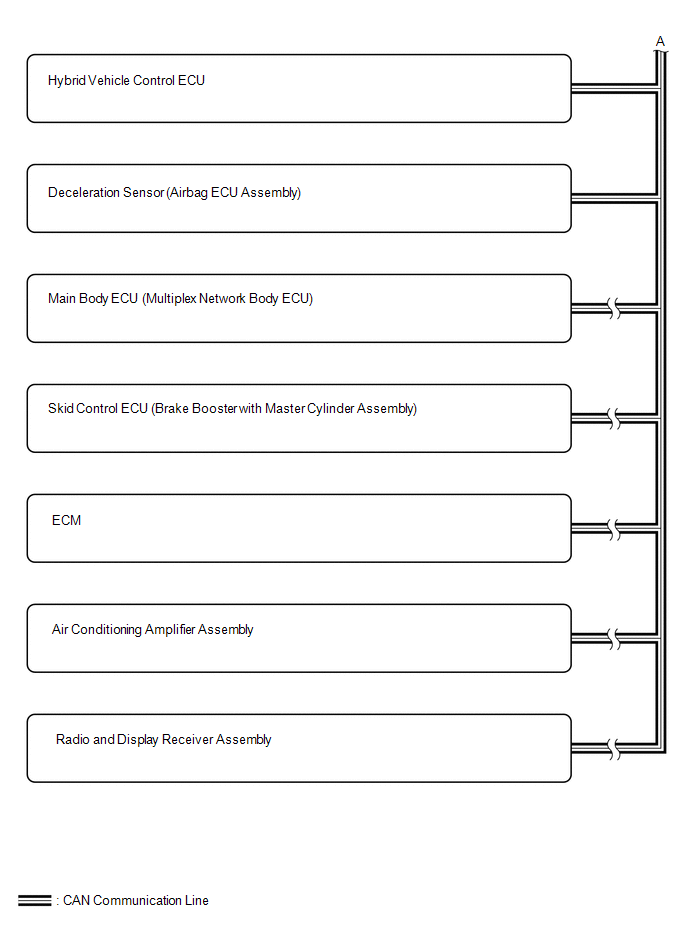
Terminals Of Ecu
TERMINALS OF ECU
CHECK PARKING BRAKE ECU (BRAKE ACTUATOR ASSEMBLY)
*a | Front view of wire harness connector (to Parking Brake ECU (Brake Actuator Assembly)) |
- | - |
(a) Disconnect the A39 parking brake ECU (brake actuator assembly) connector.
(b) Measure the voltage and resistance according to the value (s) in the table below.
Terminal No. (Symbol) | Wiring Color |
Terminal Description | Condition |
Specified Condition |
A39-9 (BEPB) - Body ground |
R - Body ground | Parking brake power supply |
Power switch off | 11 to 14 V |
A39-26 (IG) - Body ground |
B - Body ground | IG power supply |
Power switch on (IG) |
8 to 16 V |
A39-2 (EGND) - Body ground |
W-B - Body ground | Ground |
Always | Below 1 Ω |
A39-13 (POL) - Body ground |
L - Body ground | Electric parking brake switch indicator light |
- | - |
A39-14 (SWI1) - Body ground |
P - Body ground | Electric parking brake switch (electric parking brake switch assembly) |
- | - |
A39-24 (SWI2) - Body ground |
W - Body ground | Electric parking brake switch (electric parking brake switch assembly) |
- | - |
A39-20 (SWO1) - Body ground |
SB - Body ground | Electric parking brake switch (electric parking brake switch assembly) |
- | - |
A39-22 (SWO2) - Body ground |
V - Body ground | Electric parking brake switch (electric parking brake switch assembly) |
- | - |
A39-4 (MRR+) - Body ground |
LA-Y - Body ground | Parking brake motor RH (parking brake actuator assembly RH) (+) |
- | - |
A39-3 (MRR-) - Body ground |
LA-L - Body ground | Parking brake motor RH (parking brake actuator assembly RH) (-) |
- | - |
A39-7 (MRL+) - Body ground |
LA-G - Body ground | Parking brake motor LH (parking brake actuator assembly LH) (+) |
- | - |
A39-8 (MRL-) - Body ground |
LA-W - Body ground | Parking brake motor LH (parking brake actuator assembly LH) (-) |
- | - |
A39-27 (SPD) - Body ground |
L - Body ground | Vehicle speed direct input |
- | - |
A39-12 (CANH) - Body ground |
B - Body ground | CAN communication line H |
- | - |
A39-11 (CANL) - Body ground |
W - Body ground | CAN communication line L |
- | - |
Test Mode Procedure
TEST MODE PROCEDURE
*1 | Rear Disc Brake Piston |
*2 | Nut |
*a | The nut moves inward in pad replacement mode |
REAR BRAKE PAD REPLACEMENT MODE
HINT:
When
replacing the rear disc brake pad and rear disc, since the nut inside
the rear disc brake cylinder assembly is in an advanced position, it is
necessary to move the nut back inside the cylinder. The nut can be moved
back using pad replacement mode.
(a) Pad replacement mode
When Using the Techstream:
- Turn the power switch off.
- Connect the Techstream to the DLC3.
- Turn the power switch on (IG).
- Turn the Techstream on.
- Enter the following menus: Chassis / Electric Parking Brake / Utility / Check Mode.
- Follow the Techstream display and select "Next".
- Push and hold the electric parking brake switch (electric parking brake
switch assembly) to the release side for 5 seconds or more.
NOTICE:
- Make sure to perform this procedure with the power switch on (IG).
- Make sure that the brake pedal is not depressed when performing this procedure.
- When the system changes to pad replacement mode, DTC C13A7 may be
stored. If the DTC is stored, clear the DTCs after the procedure (rear
brake pad replacement, etc.) is complete.
HINT:
The
parking brake indicator light flashes (red) (0.25 seconds intervals).
After a short time, the parking brake actuator assembly operates (if the
parking brake is engaged, the motor will operate to disengage the
parking brake, and then will operate again). Once the parking brake
actuator assembly is in the pad replacement position, the parking brake
indicator light flashes (red) (1 second intervals).
Chassis > Electric Parking Brake > Utility
Tester Display |
Check Mode |
When not Using the Techstream:
- Turn the power switch off.
- Turn the power switch on (IG).
- Within 8 seconds, operate the electric parking brake switch (electric
parking brake switch assembly) to perform 3 lock side ON operations
(from off (release) to on (pull)) and then 3 release side ON operations
(from off (release) to on (push)).
NOTICE:
- If the operation is performed too quickly, the system may not respond.
If the system does not respond, perform the operation again at a slower
speed.
- The parking brake must be released.
HINT:
The parking brake indicator light (red) flashes (0.25 seconds intervals).
- Push and hold the electric parking brake switch (electric parking brake
switch assembly) to the release side for 5 seconds or more.
NOTICE:
- Make sure to perform this procedure with the power switch on (IG).
- Make sure that the brake pedal is not depressed when performing this procedure.
- When the system changes to pad replacement mode, DTC C13A7 may be
stored. If the DTC is stored, clear the DTCs after the procedure (rear
brake pad replacement, etc.) is complete.
HINT:
After a
short time passes, the parking brake actuator assembly operates (if
operated from the parking brake locked condition, the motor of the
parking brake actuator assembly is temporarily stopped after being
operated, and then operation starts again), and once the assembly
finishes operating, the parking brake indicator light (red) flashes
slowly (1 second intervals). (Nut moves back inside the cylinder and
system enters pad replacement mode).
(b) Turn the power switch off.
NOTICE:
Do
not operate the electric parking brake switch (electric parking brake
switch assembly) until the procedure is complete. If operated, the
system will return to its normal condition.
When Using the Techstream:
- Disconnect the Techstream from the DLC3.
(c) Normal condition recovery
(1)
After the procedure (rear brake pad replacement, etc.) is complete,
turn the power switch on (IG) and pull the electric parking brake switch
(electric parking brake switch assembly) to the lock side for 5 seconds
or more.
NOTICE:
- When performing work (replacing the rear brake pad, etc.), do not
operate the electric parking brake switch (electric parking brake switch
assembly) or turn the power switch on (IG) and operate the shift lever.
If the electric parking brake switch (electric parking brake switch
assembly) or shift lever is operated, the parking brake may operate and
the rear disc brake piston may fall off. Also, make sure to disconnect
the connector of the parking brake actuator assembly or disconnect the
cable from the negative (-) auxiliary battery terminal.
- When DTC C13A7 is stored, clear the DTCs.
Control Module Communication Bus OFF (U0073,U0100,U0124,U0129,U0293)
DESCRIPTION
The parking
brake ECU (brake actuator assembly) communicates with the hybrid vehicle
control ECU assembly, skid control ECU (brake booster with master
cylinder assembly) and deceleration sensor (airbag ECU assembly) via CAN
communication.
DTC No. | Detection Item |
DTC Detection Condition | Trouble Area |
Memory | Note |
U0073 | Control Module Communication Bus OFF |
Both of following conditions are met:
- Power switch on (IG)
- Bus is off (communication with other ECUs is not possible).
| CAN communication system |
DTC stored | An electric parking brake system malfunction is displayed on the multi-information display. |
U0100 | Lost Communication With ECM/PCM "A" |
Both of following conditions are met:
- Vehicle being driven at 6 km/h (4 mph) or more.
- Parking brake ECU (brake actuator assembly) cannot receive signals from the ECM for approximately 15 seconds.
|
- CAN communication system
- ECM
| DTC stored |
An electric parking brake system malfunction is displayed on the multi-information display. |
U0124 | Lost Communication With Lateral Acceleration Sensor Module |
Both of following conditions are met:
- Vehicle is being driven at 6 km/h (4 mph) or more.
- Parking brake ECU (brake actuator assembly) cannot receive signals from
the deceleration sensor (airbag ECU assembly) for approximately 15
seconds.
|
- CAN communication system
- Deceleration sensor (Airbag ECU assembly)
| DTC stored |
An electric parking brake system malfunction is displayed on the multi-information display. |
U0129 | Lost Communication with Brake System Control Module |
Both of following conditions are met:
- Power switch on (IG).
- Parking brake ECU (brake actuator assembly) cannot receive signals from
the skid control ECU (brake booster with master cylinder assembly) for
approximately 15 seconds or 30 seconds (malfunction duration differs
depending on the signal).
|
- CAN communication system
- Skid control ECU (brake booster with master cylinder assembly)
| DTC stored |
An electric parking brake system malfunction is displayed on the multi-information display. |
U0293 | Lost Communication With Hybrid Vehicle Control System |
Both of following conditions are met:
- Vehicle being driven at 6 km/h (4 mph) or more.
- Parking brake ECU cannot receive signals from the hybrid vehicle control ECU for approximately 15 seconds.
|
- CAN communication system
- Hybrid vehicle control ECU
| DTC stored |
An electric parking brake system malfunction is displayed on the multi-information display. |
PROCEDURE
1. |
GO TO CAN COMMUNICATION SYSTEM |
(a) Go to CAN communication system.
Click here
NEXT |
| END |